In the modern era, the blend of art, craftsmanship, and technology is truly mesmerizing. From hand-forged blades of ancient times to the precision-engineered tools of today, knife making has evolved considerably. Today, however, the concern isn’t just about the sharpness of a blade but also about the environmental footprint left behind in its creation. Modern knife making factories and workshops are heeding the call, introducing environmental standards to their production lines.
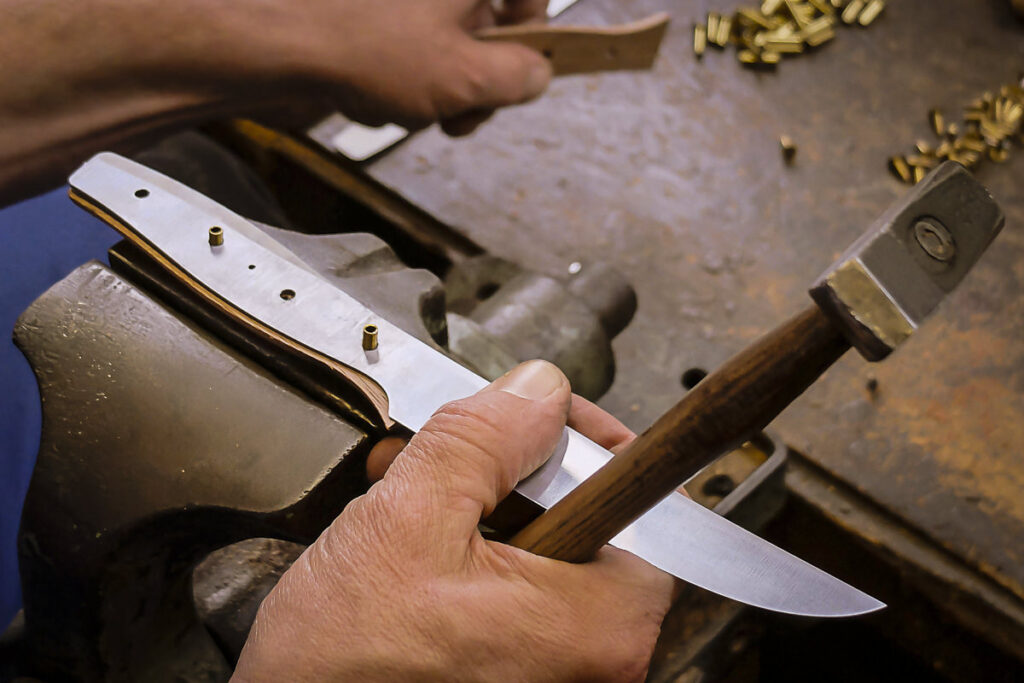
Understanding the Environmental Concerns
At the heart of the craft, every knifemaker understands the intricate dance of elements that go into creating a perfect blade. From the ancestral blacksmiths forging blades in their small workshops to the modern artisans creating custom knives with precision and flair, the journey of knife making is rich and varied. But with this journey come several environmental concerns.
Each phase, be it mining, smelting, forging, grinding, or polishing, is not just an essential step towards achieving the perfection a custom knife demands, but it also carries an environmental cost. The mining process, for instance, often leads to habitat destruction and soil erosion, while smelting can release harmful emissions into the atmosphere. Similarly, the forging process in custom knives manufacturing requires intense heat, which means a considerable energy consumption, often sourced from non-renewable resources.
Water, a vital element in knife making, especially during the cooling and tempering processes, is consumed in large quantities. This consumption further strains our already depleting freshwater sources. Additionally, as blades are crafted, shaped, and sharpened, waste in the form of metal shavings or cut-offs is generated, adding to the burden on landfills if not properly recycled.
Yet, as awareness about our planet’s fragile state grows, there’s a shift in perspective. Our collective consciousness is increasingly becoming attuned to the ecological imbalances these processes might cause. Consequently, it’s heartening to see that the community of knifemakers, especially those passionate about crafting custom knives, are not only acknowledging these environmental impacts but actively seeking sustainable and greener solutions to reduce their carbon footprint and pave the way for a more responsible and eco-friendly knife-making future.
Eco-friendly Materials and Sourcing in Knife Production
Every knife begins its journey from a raw material, and in today’s eco-conscious world, the choice of this material matters immensely. Manufacturers are making concerted efforts to find materials that tread lightly on our planet.
Recycled Steel: Steel is fundamental to knife-making. However, the extraction and processing of virgin steel can wreak environmental havoc. To counter this, there’s an increasing lean towards recycled steel. This eco-friendly alternative doesn’t just diminish the detrimental environmental effects of mining but is also more energy-efficient, using a fraction of the energy needed to produce new steel from raw iron ore.
Sustainable Handles: The handle, an extension of the blade, demands both durability and aesthetic appeal. Materials like bamboo and sustainably harvested wood have become the top choices for many knifemakers. By choosing such materials, they ensure the longevity of the product while concurrently preserving the health and integrity of our forests.
Energy Efficiency in Production
As the global focus shifts towards sustainable energy solutions, knife production factories are not far behind. Modern facilities are increasingly investing in energy-efficient machinery to reduce power consumption. Beyond that, there’s an increasing adoption of renewable energy sources, such as solar and wind, to power these factories. This shift doesn’t only reduce operational costs but more crucially, curtails the carbon footprint, ushering in a more sustainable production process.
Waste Reduction and Recycling
Every stage of knife production, from forging to final polishing, produces some waste. However, the emphasis today is on seeing this not as ‘waste’ but as ‘potential resources.’ Metal shavings, cut-offs, and other byproducts are being recycled more efficiently than ever before. Through innovative techniques and technologies, these so-called wastes are either turned into new products or reintroduced into the production cycle, thereby promoting a circular economy.
Eco-friendly Packaging
A product’s environmental impact doesn’t end with its creation. The packaging, often an afterthought in many industries, plays a pivotal role in knife production. There’s a conscious move away from plastics and other non-biodegradable materials. Instead, manufacturers are opting for recycled cardboard, minimalist designs, and biodegradable plastics. This transition ensures that the knife’s packaging complements the ethos of the product itself – efficient, high-quality, and environmentally conscious.
Embracing Digital Technology
The precision demanded in knife-making has found a robust ally in digital technology. Modern workshops are leveraging technologies such as Computer-Aided Design (CAD) and Computer Numerical Control (CNC) machines. These technologies not only augment the precision and quality of the knives but also significantly reduce material waste. By minimizing human errors, these digital tools ensure that every ounce of material is used optimally.
Community Engagement
Knifemakers today recognize that they’re part of a broader community – one that relies on the health of its environment. Many are proactively engaged with local communities, championing causes such as tree planting, clean water initiatives, and environmental education. These collaborations not only offset the environmental impacts of knife production but also foster a sense of unity, empowering communities to participate actively in crafting a greener tomorrow.
In Conclusion
The age-old craft of knife making is undergoing a green revolution. From sourcing to packaging, every step of the process is being scrutinized for its environmental impact. By embracing these changes, modern knife making factories and workshops are setting a new standard, proving that quality and sustainability can, and should, go hand in hand.
In the words of a master bladesmith, “Our knives should not only be sharp but should also reflect our sharp commitment to a better world.”